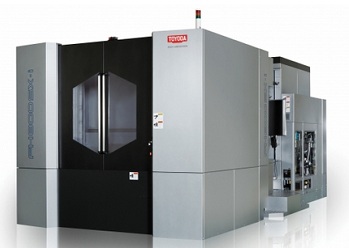
With the introduction of its latest ‘New World’ machining centre the Toyoda FH800SX-i, the company has responded to the need for more environmentally - friendly products. The FH800SX-i has an 800mm pallet and X-axis of 1450mm, Y-axis of 1250mm and Z-axis of 1550mm.
Working to its own Eco-Scale assessment indicator of 0 to 100 – the smaller the number the better - the new machine was calculated to be rated at 68.2 against the previous generation product – an overall reduction of 14%. In terms of CO2 the machine signified a reduction of 18.4%.
According to Toyoda, 2D CNC of Hinckley, in performing the Eco-Scale assessment, items were rated by Toyoda in four distinct categories: reduction, environmental maintainability, energy saving and information disclosure. In each item area it was rated against assessment points through the life-cycle of the machine.
Reduction involved its manufacture, packing, transportation and equipment application while environmental maintainability covered procurement and disposal, which also involved the use of hazardous/toxic properties, or any elements that could prove dangerous.
Energy saving covered all aspects of equipment application and its manufacture and information disclosure, the provision of information at the time of product disposal.
Such was the result for the new machine development programme that the builder reduced the number of parts by 20% – a more simple structure not only saved resource but would also contribute to higher overall reliability in service.
The reduction in coolant consumption created savings of 40% by developing a centre trough method for chip evacuation, which was sited directly below the cutting area. According to Toyoda, swarf disposal puts high demand on fixed energy, the supply of hydraulic pressure, lubricant and pneumatics to accommodate the vast amount of coolant flow required to discharge large volumes of material.
Coolant pump power requirements were also reduced by half due to the centre trough system. As a result the power of pumps could be reduced and by optimising piping and layout, this contributed to a further 10% reduction in pressure loss.
Even the number of bolts used in build were reduced by 15% due to optimisation of the design of the machine structure and a 32% reduction in cabling was achieved by utilising the field bus method giving easier connection between PLC, sensors, SOL valves and other control devices.
By changing the material in the tool magazine socket from phenol resin to Type 66 nylon, which can be recycled, this contributed to an annual material saving of 4.8t. |